Free Resources
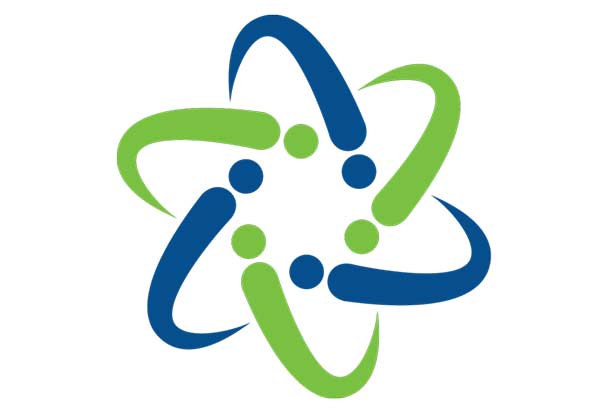
Integrated Success Inspiration
Blog
Curious about expanding your organization’s positive impact? Start by creating a workplace culture that inspires the greatness that exists within! Explore our blog for Integrated Success Inspiration.
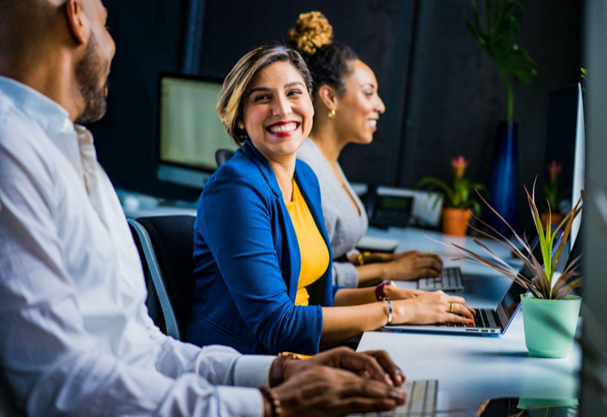
7 Keys to Cultivating a Collaborative Culture
Ebook
Download my free eBook and start elevating your workplace culture today! 7 Keys to Cultivating a Collaborative Culture. Learn strategies you can use as a senior leader to engage your team in ways that are inspiring, authentic, and productive.
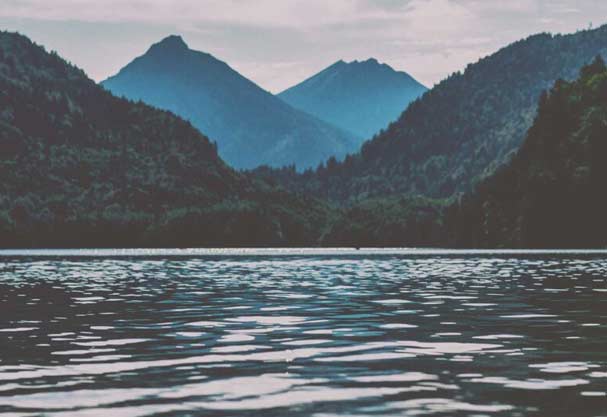
Coming
Soon
Webinar
A webinar for insightful senior leaders like you will be posted here. Check back soon!